In the realm of automotive innovation, carbon fiber has emerged as a material that promises both strength and lightweight efficiency. It appears in many components, with spoilers being a notable application. Boasting impressive performance benefits, its allure is hard to resist. Yet, as with all technologies, there are two sides to the story. This is exactly what we'll dive into today.
While the advantages are widely proclaimed, it’s important to look at the other side of the coin. From environmental impacts during production to considerations around cost, safety, and longevity, carbon fiber is not without its challenges. Let's unravel these aspects and focus on some of the less discussed issues surrounding the use of carbon fiber in cars.
Environmental Concerns
When we explore the world of carbon fiber, its environmental footprint becomes a point of notable discussion. The production of carbon fiber involves processes that are energy-intensive, primarily due to the need for high temperatures to convert raw materials into this sought-after material. This is mainly because carbon fiber production requires the pyrolysis of a polymer like polyacrylonitrile (PAN) at temperatures exceeding 1,000 degrees Celsius. That kind of heat doesn’t come cheap, either in terms of energy consumption or environmental cost. The result is significant carbon dioxide emissions, a point often glossed over in the rush to highlight its benefits.
Carbon fiber's raw material, PAN, is derived from petrochemicals, the extraction and refinement of which come with their own environmental baggage. The toxic chemicals released during production pose a hazard to workers and surrounding communities, raising ethical questions about manufacturing practices. What's alarming is that many factories are still located in places where environmental regulations may not be as stringent, exacerbating the situation. Surprisingly, an influential study from MIT cited that “carbon fiber composite production can emit up to twice the greenhouse gases compared to traditional steel or aluminum.”
This leads us to another issue: recyclability. Carbon fiber, unlike some metals, isn't easy to break down or recycle. Once its lifecycle ends in a component such as a spoiler or an aircraft part, it can contribute to landfill if not managed responsibly. Recycling methods are still evolving, but they can be costly and complex. The material's durability, while a significant advantage during its use, works against it when considering waste management options. This limitation poses a challenge in the broader narrative of reducing automotive waste.
The quest for eco-friendlier alternatives is ongoing, with researchers exploring methods to make carbon fiber production cleaner and its lifecycle more sustainable. Initiatives such as bio-based precursors or advanced recycling technologies are gaining traction. These approaches offer a glimmer of hope in mitigating the environmental impact associated with this otherwise revolutionary material. Yet, they require time and investment to become mainstream solutions. The hope is that with awareness and technological advancement, carbon fiber’s environmental impact can be minimized, balancing its high-performance allure with genuine ecological responsibility. For now, discerning consumers would do well to weigh these environmental facets when considering carbon fiber components for their vehicles.
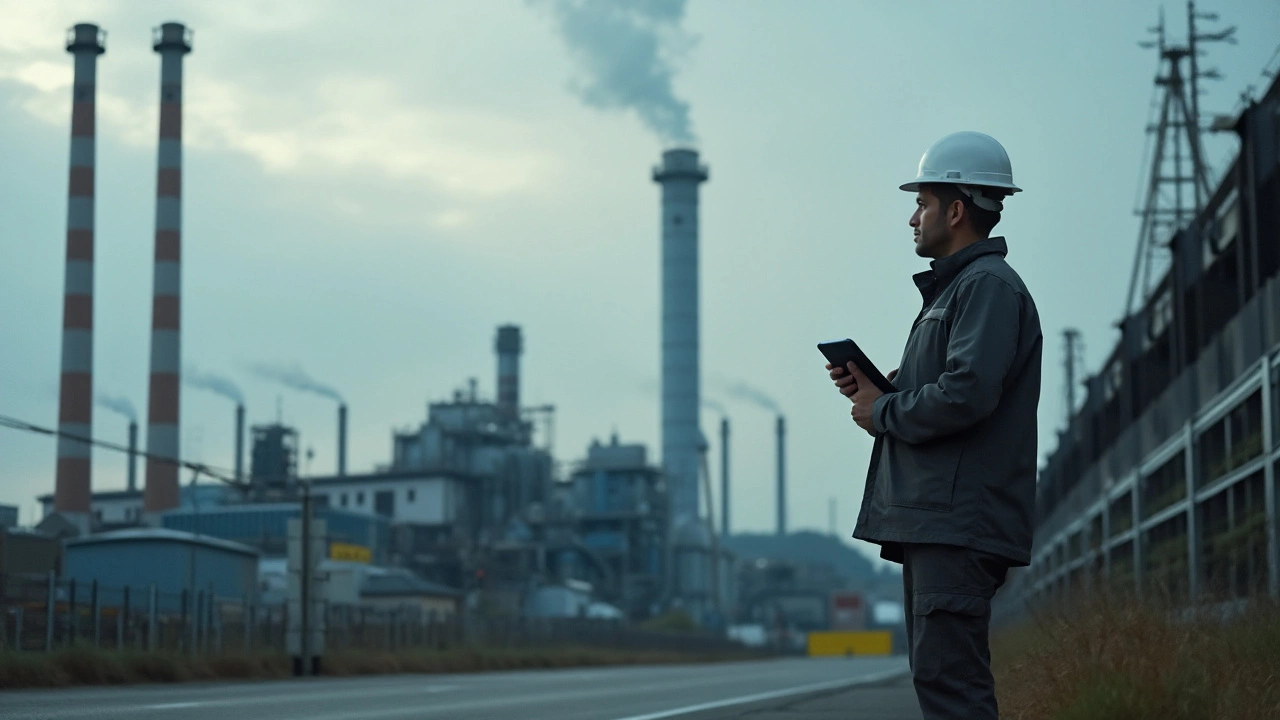
Cost Implications
The allure of carbon fiber in the world of automotive engineering is often countered by its significant cost implications. This material is renowned for its unique properties—being both strong and lightweight. However, the innovation doesn't come cheap. The production of carbon fiber is an energy-intensive process that involves the careful transformation of polyacrylonitrile, or PAN, through various stages to create the final material. These high energy requirements significantly contribute to the cost, making it more expensive than traditional materials like aluminum or steel.
One might wonder why the automotive industry is so smitten with carbon fiber, given these high costs. The answer often lies in the performance benefits that outweigh the initial investment, especially in high-end sports and luxury cars where every kilogram saved contributes dramatically to improved speed and fuel efficiency. However, for mass-market vehicles, the cost barrier remains a significant hurdle. The expense isn't solely in the material itself but also in the expertise and special equipment required to work with it. The complexity of molding and layering carbon fiber means that manufacturing processes need to be adapted, often leading to increased labor costs as well.
"The cost of carbon fiber production is a reflection of the meticulous craft required to produce a material capable of outperforming metals," notes Dr. Jenna Collins, a materials scientist specializing in composite materials.
These cost elements also impact other aspects such as repair and replacement. In contrast to metals, if a carbon fiber component suffers damage, it usually can't simply be bent back into shape or easily welded like a piece of metal. Specialized repairs or replacements are necessary, which require skilled technicians and can therefore cost a pretty penny. Not to mention, the importance of maintaining the strengths of the material without compromising on safety is paramount, often leading to entire part replacements rather than patch repairs.
Balancing Benefits with Costs
Despite the high initial costs, many automakers argue that the long-term benefits of carbon fiber justify the expense. Improved fuel efficiency due to reduced weight can lead to lower operating costs over the lifespan of the vehicle. As regulatory pressures push for lower emissions and better fuel economy, the appeal of carbon fiber surfaces again, often tipped in favor of its integration. However, this long-term equation only resonates with buyers when the benefits translate tangibly to their experience. Yet, remaining a tangible option only for luxury vehicle manufacturers means breaking into the general population becomes a challenge. The strong spoilers made from carbon fiber in sports cars are a testament to this ongoing commitment, but the journey of making carbon fiber mass-market ready continues.
Moreover, efforts continue to bring down production costs. Innovations in recycling, as well as the development of alternative precursors to PAN, promise exciting opportunities for the future. Companies are exploring new methods to reduce waste and energy consumption during production, which could significantly lower costs. Whether these advancements will make carbon fiber viable for more manufacturers remains a tale of tomorrows.
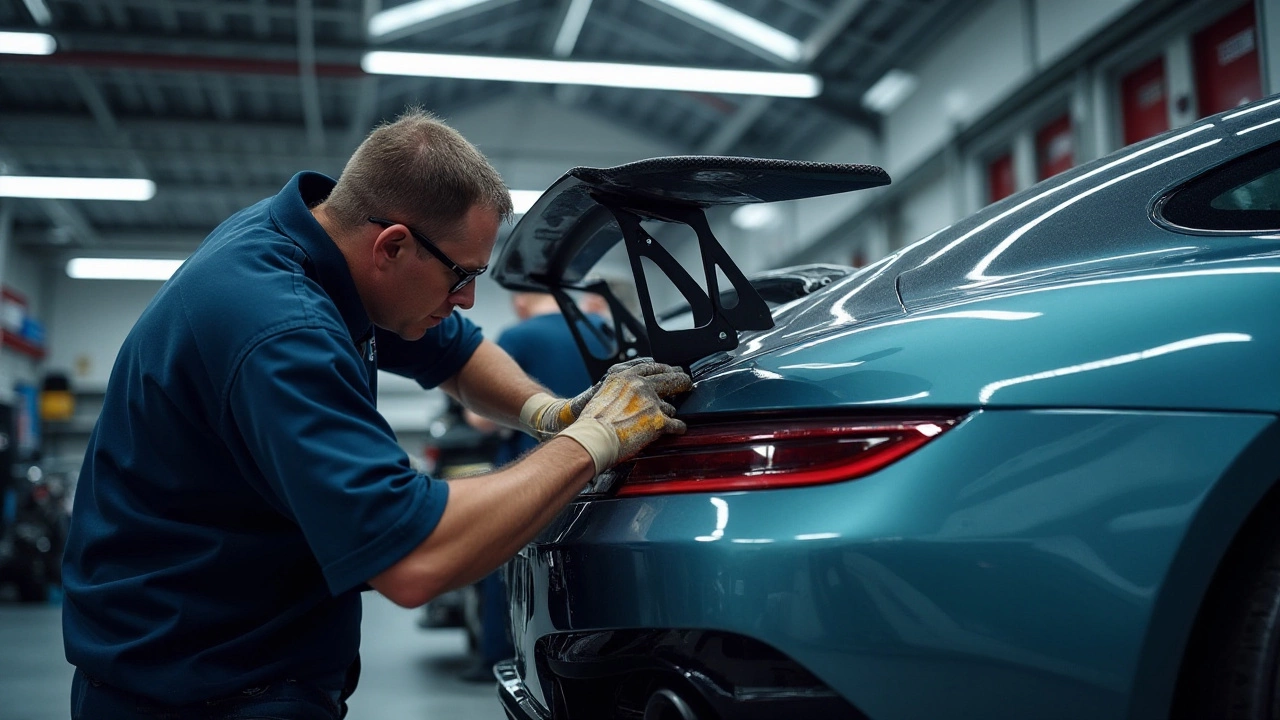
Safety Considerations
When diving into the world of carbon fiber and its applications in the automotive industry, safety is an aspect that deserves detailed attention. Known for its lightweight yet robust properties, carbon fiber is often hailed as a super material. But when we look at the safety elements, a more nuanced picture starts to emerge. For instance, during accidents, the way carbon fiber behaves can differ significantly from metals traditionally used in car manufacturing. While metals tend to crumple, absorbing impact energy, carbon fiber, although strong, can be brittle. It tends to shatter upon impact, which could pose potential safety risks. This behavior may lead to the formation of sharp shards, differing from the predictable folding of metal components.
Moreover, repairing carbon fiber spoilers and other components after an incident can also raise safety concerns. Repairing these materials requires specialized knowledge and skills, which aren't as widespread as those for traditional automotive materials. Inadequate repairs can compromise the integrity of the component, inadvertently affecting safety. Training for technicians is evolving, yet the skills gap persists. It's important to note that improper repairs could impact the overall stability of the vehicle and compromise safety performance in future driving situations.
Another layer of the safety concern pivots around the manufacturing process itself. The fibers released during the manufacturing and cutting of carbon fiber materials can pose respiratory hazards if not handled properly. Although employers ensure safety standards are maintained, it's a point worth mentioning for those involved in its production. Respiratory equipment and proper cutting methods are crucial for worker safety. Proper risk assessments and continuous monitoring of these processes are essential to protect workers’ health.
Environmental and Health Implications
The potential toxicity of carbon fiber dust cannot be overlooked. Exposure to this dust in inadequately ventilated settings may pose unknown health risks over the long term. According to a report published by the National Institute of Occupational Safety and Health, prolonged exposure to such particulates could lead to respiratory complications. With evolving research, companies are focusing on innovation in protective technologies to mitigate these risks now and in the future. This dedication is fundamental to ensuring the well-being of communities connected with the production and utilization of this remarkable material.
"Safety is the bedrock that the auto industry must build upon as it explores lightweight solutions like carbon fiber," said Dr. James Harrison, automotive safety expert from the Vehicle Technology Center. "Understanding the full scope of these materials is crucial for developing safe implementation practices."
The dynamic nature of the carbon fiber industry certainly presents safety challenges, yet also considerable potential if these are effectively managed. As its use becomes more widespread, ongoing advancements in understanding and mitigating risks are vital. This balance between innovation and caution will likely dictate the trajectory of carbon fiber's future in automotive applications.
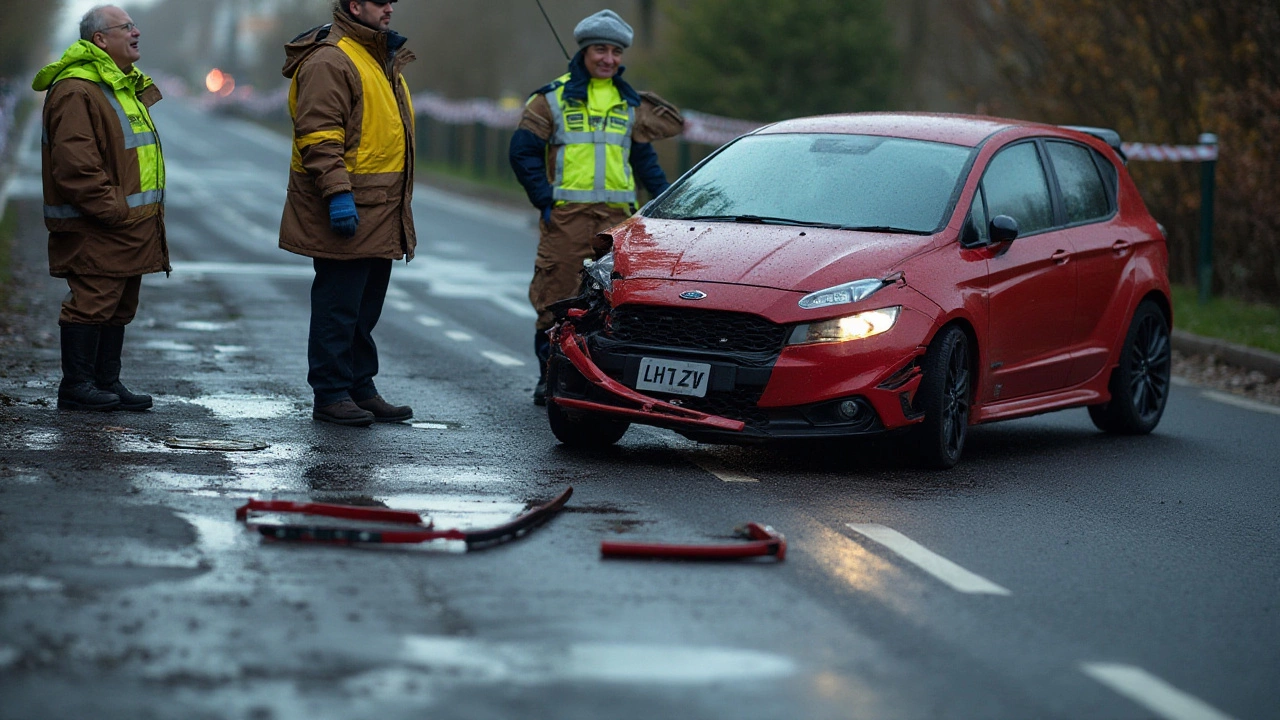
Durability and Longevity
When it comes to carbon fiber, one of its touted benefits is the material's durability and long-lasting nature. However, it is crucial to understand that while carbon fiber is known for its strength, it does have certain vulnerabilities. For car owners, investing in carbon fiber spoilers or parts should come with an understanding of these limitations.
Unlike metals that might bend or dent upon impact, carbon fiber tends to shatter. This can be particularly disadvantageous because repairs are not as straightforward as they are with metal. A minor scratch or crack, if untreated, can spread over time, compromising the integrity of the component. Not to mention, the repair process itself requires specialized knowledge and skills, often making it costly to fix.
Interestingly, when it comes to prolonged usage, carbon fiber exhibits a high resistance to corrosion, a stark contrast to metals which can rust over time. This means that in environments where moisture or salt exposure is a constant threat - such as coastal areas or regions with heavy road salting in winter - carbon fiber maintains its pristine condition where metals would deteriorate.
"Carbon fiber's resistance to elements makes it a favorite in the aerospace industry as well," notes Dr. Simon Fray, a materials engineer from AeroTech Innovations.
Yet, this doesn't make it entirely maintenance-free. UV exposure can degrade the resin holding the fibers together over time, leading to surface yellowing or fading. To combat this, manufacturers often apply a protective UV-resistant coating, but this too can wear off, necessitating periodic reapplication. Regular inspections and upkeep become essential to ensure that the components retain their performance levels and aesthetic appeal.
Long-term durability also relates to how carbon fiber is layered during production. Various processes like hand layup or automated fiber placement can influence the lifetime of the material. Proper manufacturing can extend the durability significantly, while inconsistencies during production may introduce weaknesses. As a consumer, understanding that not all carbon fiber parts are created equal can help significantly. This can, fortunately, be addressed by sourcing from reputable manufacturers and ensuring the correct installation.
Write a comment