If you've ever wondered whether a 10W laser can cut through carbon fiber, you're not alone. It sounds like a neat trick, especially if you're dabbling in creating sleek carbon fiber spoilers for cars. But spoiler alert (pun intended), it's more complicated than just firing up a laser and getting crafty.
First things first, let's chat about laser power. A 10W laser is considered pretty low in the grand scheme of industrial cutters. For delicate tasks like engraving or cutting thin materials, it shines. But when it comes to something as tough and layered as carbon fiber? Now we've got a challenge on our hands. The fibers are known for their strength and heat resistance, which means they don't just give in to any old light beam.
- Understanding Laser Power
- Carbon Fiber Properties
- The 10W Laser Challenge
- Real-World Applications
- Safety and Equipment
- Alternatives to Consider
Understanding Laser Power
Alright, let’s talk lasers. The power of a laser—measured in watts—tells us how much energy it puts out. So, when you hear about a 10W laser, you’re dealing with a pretty modest output compared to the big boys in industrial settings.
For perspective, lasers used in industrial cutting tend to crank out anywhere from 50W to several kilowatts. These massive figures are necessary because tougher materials, like metals and dense composites, require a lot more juice to cut through. Carbon fiber, despite being lightweight, falls under the 'tough material' category.
But don't count the 10W laser out just yet. It performs super well for detail work like engraving or cutting thinner materials, such as certain plastics or even wood. Its lower power output actually gives it an edge in precision, which might be handy if you're working on intricate designs or prototypes.
- Key advantage: Low power means less risk of accidental damage when working with delicate or heat-sensitive materials.
- Key limitation: Struggles with thicker or more robust materials such as carbon fiber.
Understanding this fine balance between power and application is vital, especially if you’re exploring creative avenues like crafting carbon fiber spoilers. While it might not slice through carbon fiber like butter, it certainly has its niche in the laser world!
Carbon Fiber Properties
Carbon fiber is kind of like the superhero of materials. It's super strong and lightweight, making it a favorite for folks in the auto industry, especially when it comes to carbon fiber spoilers. But what makes it so special?
For starters, carbon fiber is made up of thin, strong crystalline filaments of carbon. These tiny fibers are woven together to make a fabric or combined with other materials to form a composite. The result? A material that's five times stronger than steel and a fraction of the weight.
Here's the kicker, though—carbon fiber has incredible stiffness and high tensile strength. That means it can take a lot of pulling or stretching without breaking. Plus, it has low thermal expansion, so it won’t expand or contract much with temperature changes, which is great news if you're using it in environments where other materials might warp or break.
But before you get all starry-eyed about its strength, remember that it's also very resistant to heat. This heat resistance can be a bit of a buzzkill when you're trying to cut it neatly, especially with a low-power laser like a 10W one. It's like trying to cut a diamond with a plastic knife—not exactly gonna happen easily.
Another fun fact: Carbon fiber isn't just one-size-fits-all. Depending on how it's made and the types of fibers or matrix used, it can have varied properties. This versatility is part of what makes carbon fiber so valuable—but also a bit challenging when you're trying to cut it exactly the way you want.
Here's a little data to chew on:
Property | Value |
---|---|
Density | 1.75 - 1.93 g/cm³ |
Tensile Strength | ~5000 MPa |
Elastic Modulus | ~230 GPa |
The 10W Laser Challenge
Okay, so you're thinking about using a 10W laser to cut carbon fiber for your latest project. Let’s break down the challenge. Carbon fiber is one tough cookie. It's made from woven strands of carbon, which gives it an incredible strength-to-weight ratio. This toughness is exactly why it's perfect for carbon fiber spoilers on high-performance cars. But it also means you need some serious power to cut through it cleanly.
Now, a 10W laser might sound like it packs a punch, but in the world of laser cutting, that's more like a featherweight. Typically, you'd need a laser with much higher wattage—think in the hundreds or even thousands of watts—for the laser cutting tasks involving materials as durable as carbon fiber.
Why doesn’t the 10W laser make the cut, so to speak? The energy it puts out just doesn’t have the oomph to slice through the dense weave of the fiber. It can sometimes singe the material or even burn the edges rather than cleanly cutting them. Plus, the heat produced can mess with the resin binding the fibers, potentially ruining the piece you're working on.
So, while a 10W laser might be awesome for paper, fabric, or even thin plastic, when it comes to carbon fiber, it’s like bringing a butter knife to a steak party. If you're serious about cutting carbon fiber, you’ll want to explore more powerful laser systems or alternative tools like CNC machines that can handle those strong, heat-resistant fibers with precision.
Bottom line? For those sleek carbon fiber spoilers, you’re better off researching other options. Your 10W laser has its benefits, just maybe not in cutting carbon fiber sheets.
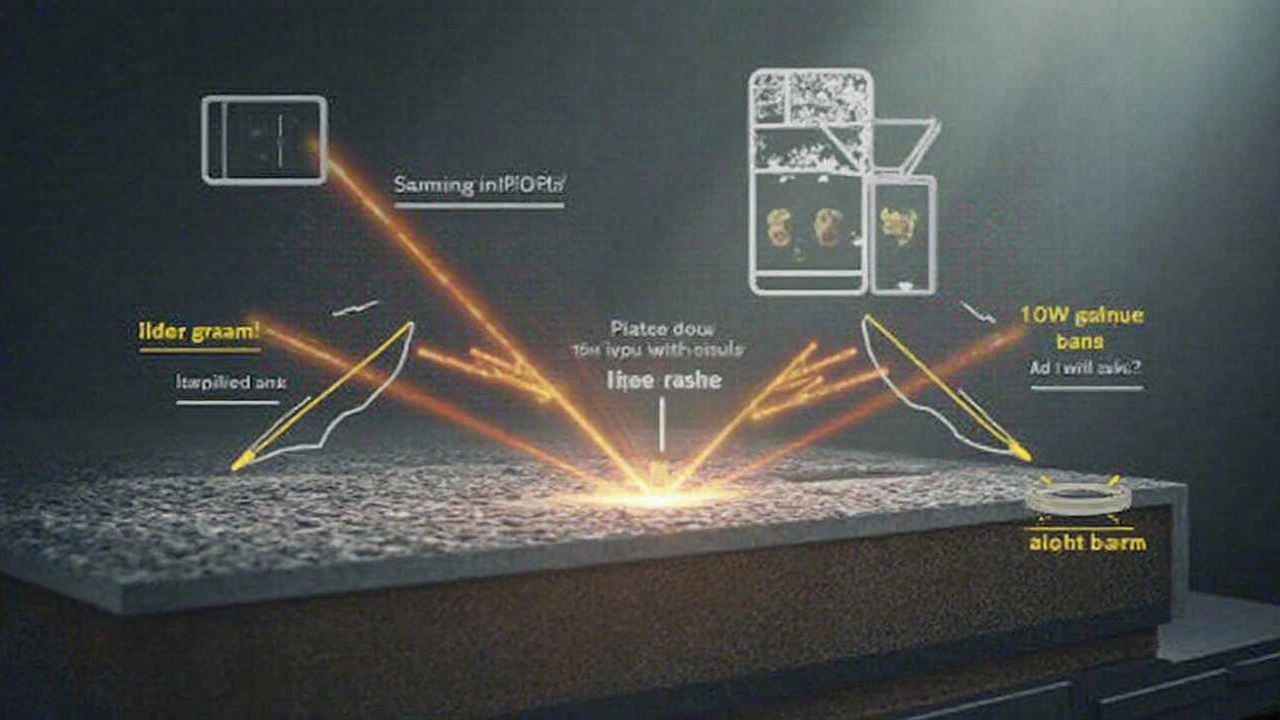
Real-World Applications
Before diving into the specifics of whether a 10W laser can slice through carbon fiber, it's crucial to grasp where and how laser cutting makes a mark in everyday life. In the auto industry, especially in customizing carbon fiber spoilers, laser cutting can be a game-changer when done right. But the typical tools aren’t low-powered lasers, that's for sure.
You'll most often see high-powered lasers (think in the hundreds of watts) making clean, precise cuts through carbon fiber sheets. These tools are used by pros to achieve the perfect cut needed for aerodynamic car parts. The task demands power and finesse because the layered structure of carbon fiber doesn't respond well to low-heat inputs. A 10W laser might handle thin layers or specific composite versions but isn’t a go-to for thick or high-grade carbon fiber, which is generally the choice for car mods.
Here's a snapshot of why higher-powered lasers are preferred in certain settings:
- Efficiency: High-wattage lasers cut quickly, reducing the time needed for each piece.
- Precision: They offer a clean edge with minimal fraying, which is vital when you're adding a visual component like a spoiler.
- Durability: Proper cuts ensure that the final product maintains its strength and integrity, a must-have for racing performance or street durability.
For hobbyists or small-scale projects, however, a 10W laser could potentially be used for engraving or cutting thin laminates or veneers that mimic carbon fiber. If you're trying to add custom designs or logos onto a pre-made spoiler, this lower wattage can make your job easier without degrading the carbon fiber's performance.
So, while a 10W laser shines for smaller, detailed projects, it's just not the tool for cutting carbon fiber sheets used for spoilers. If you're dead set on laser cutting carbon fiber, consider investing in tools with more power or finding a service with industrial-grade equipment.
Safety and Equipment
Playing with laser cutting tools is no joke, especially when dealing with carbon fiber. You gotta be smart and stay safe! Carbon fiber dust is notorious for being nasty if inhaled, and the fumes from cutting can be harmful, too. So, wearing the right protective gear like a good-quality respirator is a must.
When setting up your workspace for cutting carbon fiber with a 10W laser, ventilation is key. Make sure your area is well-ventilated or has a fume extractor handy. This will help control and remove those pesky airborne particles and toxic fumes. Seriously, you don’t want to skip this step!
As for equipment, you need a laser cutter that's reliable and comes with adjustable settings. Constantly fiddling with power and speed settings can help you avoid overheating or damaging the material. Plus, using a cooling system with your setup might be worth considering—anything to help keep things from going south.
Carbon fiber isn't something you approach with the same mindset as, say, simple wood projects. Understanding the risks and managing them with the right equipment ensures not just a successful cut, but also keeps you out of harm’s way.
Here's a quick checklist to get you started with safety in mind:
- Invest in a high-quality respirator and protective eyewear.
- Ensure proper ventilation or use a fume extractor.
- Regularly check and adjust your laser cutter's power and speed settings.
- Consider using a cooling system to manage heat buildup.
- Keep a fire extinguisher nearby just in case things get a bit too heated!
Alternatives to Consider
So, if a 10W laser is playing hard to get with your carbon fiber, what are the other cards you can play? Well, you might want to look into some beefier options.
First off, higher power lasers, like a 40W or even 100W, can do the trick. These bad boys can slice through carbon fiber more effectively, thanks to a stronger beam that can handle this tough material. They're pricier, but if you're serious about cutting carbon fiber regularly, it's a solid investment.
But lasers aren't the only way to skin this cat. Ever heard of waterjet cutting? This method uses a high-pressure stream of water mixed with abrasive materials. It’s super precise and doesn’t generate heat, so you won’t have to worry about damaging the carbon fiber with excess heat.
Then there's CNC routing, a popular choice for cutting various materials, including carbon fiber. With the right tooling, a CNC router can make clean and precise cuts. Just make sure you’ve got proper bits designed for carbon fiber to avoid splintering.
Now, if you're not up for investing in new gear, outsourcing is an option. There are professional shops equipped with industrial-grade lasers and other cutting tools. Let the pros handle it, and save yourself the hassle of trial and error.
In short, while a 10W laser might not be the perfect match for cutting carbon fiber alone, these alternatives offer a range of possibilities, depending on your project needs and budget.
Write a comment